Directeur Technique

Comprendre le contexte
Tom souhaite augmenter la capacité de production d'une ligne existante. Dans son poste de directeur technique, une des missions nécessite de trouver des nouvelles technique pour optimiser les processus de production. Actuellement, cette ligne, conçue pour produire jusqu'à 200 unités par minute, fonctionne à seulement 75% de son potentiel théorique, soit 150 unités par minute.
Plusieurs problèmes contribuent à cette sous-performance :
-
Arrêts fréquents : Les pannes imprévues et les défaillances techniques représentent 10 à 15% du temps d’arrêt total.
-
Taux de rejet élevé : Environ 5% des produits fabriqués ne respectent pas les critères de qualité, ce qui entraîne des pertes matérielles significatives.
-
Temps de changement de format : Les changements de matières premières ou de formats de produits ralentissent considérablement la production, avec des durées moyennes de 20 minutes par opération.
-
Coordination insuffisante : Un manque de communication entre les équipes de maintenance, de production, et de qualité provoque des retards dans l’identification et la résolution des problèmes.
Comprendre les enjeux de Tom
Directeur technique
Tom cherche une stratégie claire et efficace pour éliminer ces inefficacités et atteindre une capacité de production optimale, tout en maintenant un niveau de qualité élevé.
-
Augmentation de la capacité de production : Passer de 150 à au moins 180 unités par minute tout en maintenant la qualité des produits.
-
Réduction des temps d’arrêt : Minimiser les pannes en mettant en place une maintenance prédictive efficace et en améliorant la réactivité des équipes.
-
Diminution du taux de rejet : Réduire le taux de rejet à moins de 2% pour limiter les pertes matérielles et assurer la conformité des produits.
-
Optimisation des temps de changement de format : Passer de 20 minutes à moins de 10 minutes par opération pour maximiser le temps de production effectif.
-
Renforcement de la coordination inter-équipes : Améliorer la communication et la collaboration entre les différents départements pour assurer une prise de décision rapide et pertinente.
-
Suivi des performances en temps réel : Mettre en place des outils de monitoring pour analyser les performances et ajuster les paramètres de la ligne en temps réel.
Le rôle clé du coordinateur technique chez FSE INDUSTRY dans le succès du Directeur Technique
1. Analyse initiale et définition des priorités
L'audit des processus existants est une étape essentielle pour identifier les leviers d'amélioration d'une ligne de production. Il consiste à analyser en détail les performances actuelles, notamment la capacité réelle, le taux de rejets, les temps d’arrêt et les durées de changement de format. Cette analyse permet de repérer les goulets d'étranglement et les points critiques qui freinent l’efficacité. En parallèle, l’examen des données historiques aide à identifier les causes récurrentes des pannes et des ralentissements. Un échange avec les opérateurs est également indispensable pour comprendre les difficultés rencontrées sur le terrain et recueillir des suggestions d'amélioration directement issues de leur expérience.
Une fois ces éléments analysés, il est nécessaire de prioriser les actions à mettre en place. En collaboration avec le directeur technique, il faut définir les objectifs stratégiques, qu'il s'agisse d’augmenter la capacité de production ou de réduire les pannes. Chaque amélioration doit être accompagnée d’objectifs mesurables et réalistes, comme atteindre une cadence de 180 unités par minute en six mois. Cette démarche structurée permet d’optimiser progressivement les performances tout en garantissant la qualité et la fiabilité des opérations.
2. Augmentation de la capacité de production
L'optimisation des paramètres machines est une étape clé pour améliorer la performance d'une ligne de production. En collaboration avec les équipes d’automatisme, il est essentiel d’ajuster finement les réglages des équipements, notamment en optimisant les vitesses et les cadences de production. Cette démarche permet d’exploiter pleinement le potentiel des machines tout en garantissant la stabilité et la qualité du processus. Par ailleurs, l’identification des équipements sous-performant permet d’anticiper d’éventuels dysfonctionnements et d’envisager des améliorations techniques adaptées.
En parallèle, la formation des opérateurs joue un rôle déterminant dans l’optimisation des performances. En leur transmettant les meilleures pratiques et en renforçant leur compréhension des réglages et des limites des machines, ils deviennent plus autonomes et réactifs face aux variations de production. Une équipe bien formée est capable de prévenir les erreurs, de limiter les arrêts non planifiés et d’assurer une production plus fluide et efficace.
Enfin, l’évaluation du parc machine peut révéler la nécessité d’ajouter ou de remplacer certains équipements. Lorsque les optimisations ne suffisent plus à atteindre les objectifs de performance, il est pertinent d’étudier des solutions d’investissement pour moderniser ou automatiser certaines étapes critiques du processus. Cette démarche permet non seulement d’améliorer la productivité, mais aussi d’assurer une meilleure fiabilité et une réduction des coûts à long terme.
3. Réduction des temps d’arrêt
La mise en place d’une maintenance prédictive permet d’anticiper les défaillances et d’optimiser la disponibilité des équipements. L’installation de capteurs IoT permet de surveiller en temps réel l’état des machines et de détecter les premiers signes d’usure ou d’anomalie. Associé à un logiciel de gestion de maintenance assistée par ordinateur (GMAO), ce système facilite la planification des interventions avant qu’une panne ne survienne, réduisant ainsi les temps d’arrêt imprévus et améliorant la fiabilité des installations.
Parallèlement, l’amélioration de la réactivité des équipes est essentielle pour limiter l’impact des incidents techniques. La mise en place de processus d’alerte en temps réel permet d’informer immédiatement les équipes concernées en cas de dysfonctionnement. De plus, l’élaboration d’un protocole clair et structuré pour le diagnostic et l’intervention réduit considérablement le temps nécessaire pour identifier et résoudre les problèmes, garantissant ainsi une reprise rapide de la production.
4. Diminution du taux de rejet
L’analyse des causes des rejets est une étape essentielle pour améliorer la qualité de production. Il s’agit de recueillir et d’étudier les données des produits non conformes afin d’identifier les défauts récurrents. Cette démarche inclut l’examen des paramètres influençant la qualité, tels que les matières premières utilisées, les réglages machines et les conditions de production. Une compréhension approfondie de ces éléments permet de cibler précisément les sources de non-conformité et d’apporter des solutions adaptées.
Pour optimiser les contrôles qualité, il est pertinent d’automatiser les inspections en ligne grâce à des technologies comme la vision industrielle et les capteurs intelligents. Ces outils permettent une détection plus rapide et plus précise des anomalies, réduisant ainsi les erreurs humaines. Par ailleurs, des ajustements techniques ou organisationnels peuvent être mis en place afin d’améliorer la fiabilité des contrôles et limiter les écarts de production.
Enfin, la formation des équipes sur les standards qualité joue un rôle clé dans la réduction des rejets. Sensibiliser les opérateurs aux critères de conformité et leur faire comprendre l’impact des non-conformités sur les coûts de production permet d’instaurer une culture qualité forte. Une meilleure implication des équipes dans le respect des exigences qualité contribue ainsi à une amélioration durable des performances industrielles.

Remplisseuse

Groupe froid
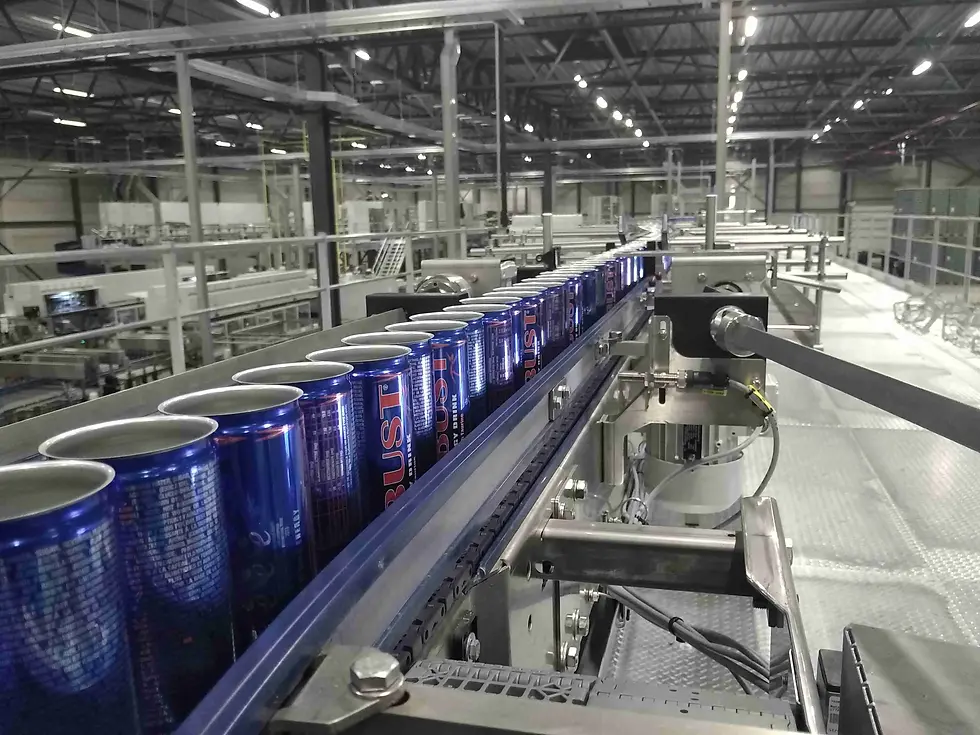
Ligne canette

Remplisseuse
5. Optimisation des temps de changement de format
L’analyse des processus actuels est une première étape essentielle pour optimiser les changements de format. Il s’agit d’étudier en détail chaque étape afin d’identifier les actions inutiles ou chronophages qui ralentissent l’opération. Cette approche permet de repérer les points d’amélioration et de définir des leviers d’optimisation pour réduire le temps d’arrêt des machines.
La standardisation des procédures joue un rôle clé dans l’amélioration de l’efficacité. En créant des checklists simplifiées et en normalisant les outils nécessaires pour chaque format, on garantit une meilleure organisation du travail et une exécution plus fluide des changements. Une méthodologie claire et reproductible permet d’éviter les erreurs et d’améliorer la rapidité d’exécution.
La formation et la simulation sont également des éléments essentiels pour rendre les équipes plus efficaces. En leur apprenant les bonnes pratiques et en organisant des exercices pratiques, les opérateurs gagnent en rapidité et en précision. La mise en situation permet aussi d’identifier les points de blocage et d’ajuster les procédures en conséquence pour un gain de temps significatif.
Enfin, l’automatisation partielle peut être une solution pertinente pour accélérer le processus. L’évaluation de technologies comme les réglages automatiques ou les outils auto-ajustables permettrait de limiter les interventions manuelles et d’améliorer la répétabilité des changements de format. Une telle approche réduit les risques d’erreur et contribue à une production plus fluide et performante.
6. Renforcement de la coordination inter-équipes
La centralisation de la communication est essentielle pour améliorer la coordination entre les équipes. L’utilisation d’outils collaboratifs comme Slack, Teams ou la suite google permet de centraliser les échanges et d’assurer un suivi en temps réel des tâches et des projets. En complément, des réunions de coordination hebdomadaires doivent être organisées pour synchroniser les actions et aligner les priorités de chacun.
Pour fluidifier encore davantage les échanges, il est important de désigner des points de contact clés dans chaque département. Ces référents serviront de relais d’information et faciliteront la transmission des consignes et des retours entre les équipes. Cette approche permet d’éviter les pertes d’information et d’assurer une prise de décision plus rapide et efficace.
Enfin, encourager la collaboration passe par l’organisation d'atelier réguliers. Ces sessions sont l’occasion de partager les bonnes pratiques, de résoudre collectivement des problématiques et de renforcer l’esprit d’équipe. En favorisant un environnement de travail plus coopératif, les équipes gagnent en efficacité et en cohésion, ce qui impacte positivement la performance globale de l’entreprise.
7. Suivi des performances en temps réel
La mise en place d’un système de monitoring permet un suivi précis et en temps réel des performances de la ligne de production. L’installation d’écrans directement sur la ligne affiche les indicateurs clés tels que la cadence, le taux de rejet et la disponibilité des équipements. En parallèle, l’utilisation d’outils de supervision comme SCADA ou MES facilite la collecte et l’analyse des données, garantissant une meilleure visibilité sur l’efficacité des opérations.
Une analyse régulière des données est essentielle pour assurer une amélioration continue. La génération de rapports automatiques hebdomadaires et mensuels permet de suivre l’évolution des performances et de détecter rapidement les écarts par rapport aux objectifs fixés. En identifiant ces écarts à temps, il devient possible de mettre en place des actions correctives immédiates pour optimiser la production et réduire les pertes.
Enfin, un retour d’information constant aux équipes est fondamental pour maintenir leur engagement. En partageant les données de performance avec les opérateurs et les responsables de production, ceux-ci prennent conscience de leur impact sur l’efficacité globale. Cette transparence encourage une dynamique d’amélioration continue et favorise l’implication de chacun dans l’optimisation des processus.
8. Suivi des résultats et ajustements
L’évaluation des progrès permet de mesurer l’impact des actions mises en place en comparant les données avant et après leur application. L’analyse des indicateurs clés, tels que l’augmentation de la production ou la réduction des arrêts, aide à quantifier les améliorations obtenues. Ce suivi permet également d’identifier de nouvelles opportunités d’optimisation pour poursuivre l’amélioration continue.
En fonction des résultats observés et des retours des équipes, la stratégie peut être ajustée afin de maximiser l’efficacité des actions mises en œuvre. Il peut s’agir de redéfinir les priorités, d’adapter les ressources ou de tester de nouvelles solutions pour atteindre les objectifs fixés. Cette approche flexible garantit une amélioration constante des performances industrielles.
Conclusion
Ce plan structuré permet au coordinateur technique de jouer un rôle clé en soutenant le directeur technique dans l’amélioration des performances globales, tout en mettant à profit ses compétences en organisation, supervision et gestion technique.
Vous souhaitez approfondir un point en particulier ?
Réduction significative des coûts liés aux rejets et aux arrêts
Ligne de production plus fiable et performante
Equipe engagée dans l’amélioration continue
Capacité de production augmentée
Bénéfices
CONTACT
Nous contacter
Téléphone : +33 (0)6 02 10 71 32
Email : contact@fseindustry.com
Adresse
6 Chemin du vieux colombier
83130 LA GARDE
France