FSE
INDUSTRY
Technical Director

Understanding the context
Tom wants to increase the production capacity of an existing line. In his role as Technical Director, one of his key missions is to find new techniques to optimize production processes. Currently, this line, designed to produce up to 200 units per minute, is operating at only 75% of its theoretical capacity, delivering just 150 units per minute.
Several issues contribute to this underperformance :
-
Frequent stoppages : Unplanned breakdowns and technical failures account for 10 to 15% of total downtime.
-
High rejection rate : Approximately 5% of the products manufactured fail to meet quality standards, leading to significant material losses.
-
Format changeover times : Switching raw materials or products formats significantly slows down production, with average changeover times of 20 minutres per operation.
-
Lack of coordination : Poor communication between maintenance, production, and quality teams causes delays in identifying and resolving problems.
​​
Understanding Tom's challenges
Technical director
​​​​Tom is looking for a clear and effective strategy to eliminate inefficiencies and reach optimal production capacity while maintaining a high level of quality.
​
-
Increase production capacity : Raise output from 150 to at least 180 units per minute while maintaining product quality.
-
Reduce downtime : Minimize breakdowns by implementing effective predictive maintenance and improving team responsiveness.
-
Lower the rejection rate : Reduce the rejection rate to below 2% to limit material losses and ensure product compliance.
-
Optimize changeover times : Reduce changeover duration from 20 minutes to under 10 minutes per operation to maximize effective production time.
-
Strengthen cross-functional coordination : Improve communication and collaboration between departments to enable faster and more effective decision-making.
-
Real-time performance monitoring : Implement monitoring tools to analyze performance and adjust line parameters in real time.
The key role of the technical coordinator at FSE INDUSTRY in supporting the success of the Technical Director
​
1. Initial analysis and priority setting​
Auditing existing processes is a crucial step in identifying areas for improvement on a production line. This involves a detailed analysis of current performance, including actual capacity, rejection rates, downtime, and format change durations. This analysis helps pinpoint bottlenecks and critical issues that hinder efficiency. At the same time, reviewing historical data helps identify recurring causes of breakdowns and slowdowns. Engaging with operators is also essential to understand the difficulties they face on the ground and to gather improvement suggestions based on their hands-on experience.
​
Once this information has been analyzed, actions must be prioritized. In collaboration with the Technical Director, strategic objectives should be defined, whether the goal is to increase production capacity or reduce equipment failures. Each improvement initiative must be accompanied by measurable and realistic goals, such as reaching a throughput of 180 units per minute within six months. This structured approach enables progressive performance optimization while maintaining quality and operational reliability.
​
2. Increasing production capacity​
​
Optimizing machine parameters is a key step in enhancing production line performance. In collaboration with automation teams, it is vital to fine-tune equipment settings, particularly by optimizing speed and throughput. This approach allows the full potential of the machines to be leveraged while ensuring process stability and product quality. Identifying underperforming equipment also helps anticipate potential malfunctions and implement suitable technical improvements.
​
Simultaneously, operator training plays a decisive role in performance optimization. By sharing best practices and reinforcing their understanding of machine settings and limitations, operators become more autonomous and responsive to production changes. A well-trained team can prevent errors, limit unplanned downtimes, and ensure smoother, more efficient production.
​
Finally, evaluating the equipment fleet may reveal the need to add or replace certain machines. When optimizations alone are not enough to achieve performance goals, it becomes relevant to explore investment opportunities to modernize or automate critical stages of the process. This approach not only boosts productivity but also enhances reliability and reduces long-term costs.
​
3. Reducing downtime
​​
Implementing predictive maintenance helps anticipate failures and maximize equipment availability. Installing IoT sensors enables real-time monitoring of machine status and early detection of wear or anomalies. Combined with Computerized Maintenance Management System (CMMS) software, this setup facilitates maintenance scheduling before breakdowns occur, thereby reducing unplanned downtime and improving system reliability.
​
In parallel, enhancing team responsiveness is critical to minimizing the impact of technical incidents. Setting up real-time alert processes ensures immediate notification to the relevant teams in case of malfunction. Additionally, creating a clear and structured protocol for diagnostics and interventions significantly reduces the time required to identify and resolve issues, ensuring rapid production recovery.
​
4. Lowering the rejection rate​
​
Analyzing the causes of rejections is a fundamental step in improving production quality. This involves collecting and examining data on non-compliant products to identify recurring defects. The process includes evaluating parameters that influence quality, such as raw materials, machine settings, and production conditions. A thorough understanding of these elements enables accurate targeting of non-conformity sources and the implementation of appropriate solutions.
​
To optimize quality control, it is beneficial to automate in-line inspections using technologies such as machine vision and smart sensors. These tools allow faster and more precise anomaly detection, reducing human error. Additionally, technical or organizational adjustments can be made to enhance inspection reliability and minimize production deviations.
​
Finally, training teams on quality standards is crucial to reducing rejections. Raising operator awareness of compliance criteria and helping them understand the cost implications of non-conformities fosters a strong quality culture. Better team engagement in meeting quality requirements contributes to the sustainable improvement of industrial performance.

Remplisseuse

Groupe froid
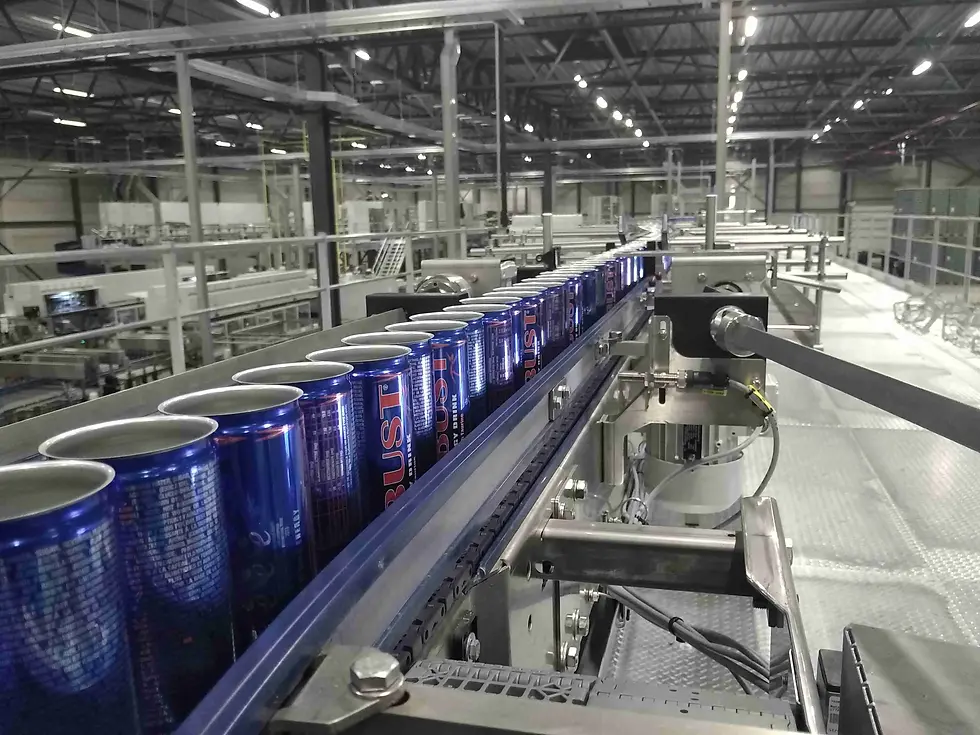
Ligne canette

Remplisseuse
5. Optimizing format changeover times
​​
Analyzing current processes is the first essential step to optimizing format changeovers. Each step should be examined in detail to identify unnecessary or time-consuming actions that slow down operations. This approach highlights improvement opportunities and defines levers to reduce machine downtime.
​
Standardizing procedures plays a key role in improving efficiency. By creating simplified checklists and standardizing the tools required for each format, work organization is improved, and format changes are executed more smoothly. A clear and repeatable methodology helps prevent errors and speeds up execution.
​
Training and simulation are also essential to make teams more effective. Teaching best practices and organizing practical exercises allows operators to become quicker and more precise. Hands-on training helps identify bottlenecks and adjust procedures accordingly for significant time savings.
​
Finally, partial automation can be a relevant solution to speed up the process. Evaluating technologies such as automatic settings or self-adjusting tools can reduce manual intervention and enhance repeatability during changeovers. This approach lowers the risk of errors and contributes to smoother, higher-performing production.
​
6. Strengthening cross-functional coordination
​​
Centralizing communication is essential for improving coordination among teams. Collaborative tools like Slack, Teams, or Google Workspace help centralize exchanges and enable real-time tracking of tasks and projects. Weekly coordination meetings should also be held to synchronize actions and align everyone's priorities.
​
To further streamline communication, it is important to designate key contacts in each department. These liaisons act as communication relays and help ensure instructions and feedback are shared effectively. This approach prevents information loss and ensures faster, more effective decision-making.
​
Lastly, fostering collaboration involves organizing regular workshops. These sessions provide an opportunity to share best practices, resolve problems collectively, and strengthen team spirit. By promoting a cooperative work environment, teams become more efficient and cohesive, positively impacting overall company performance.
​
7. Real-time performance monitoring​
​
Implementing a monitoring system allows for accurate, real-time tracking of production line performance. Installing screens directly on the line displays key indicators such as speed, rejection rate, and equipment availability. At the same time, supervision tools like SCADA or MES facilitate data collection and analysis, offering better visibility into operational efficiency.
​
Regular data analysis is essential for ensuring continuous improvement. Automatically generated weekly and monthly reports help track performance trends and quickly identify deviations from target objectives. Detecting these gaps in time enables immediate corrective actions to optimize production and reduce losses.
​
Finally, constant feedback to teams is crucial for maintaining engagement. Sharing performance data with operators and production managers helps them understand their impact on overall efficiency. This transparency promotes a culture of continuous improvement and encourages everyone to contribute to process optimization.
​
8. Results tracking and adjustments​
​
Progress evaluation helps measure the impact of actions taken by comparing data before and after implementation. Analyzing key indicators such as production increases or downtime reduction helps quantify improvements. This tracking also identifies new optimization opportunities to further drive continuous improvement.
​
Based on observed results and team feedback, the strategy can be adjusted to maximize the effectiveness of implemented actions. This may involve redefining priorities, reallocating resources, or testing new solutions to achieve set goals. This flexible approach ensures continuous enhancement of industrial performance.
​
​​​​​
Conclusion
This structured plan enables the technical coordinator to play a key role in supporting the Technical Director in improving overall performance, leveraging their expertise in organization, supervision, and technical management.
Would you like to explore one of these points in more detail?
Significant reduction in costs related to rejections and downtime
More reliable and efficient production line
Team committed to continuous improvement
Increased production capacity
Benefits
CONTACT
Contact us
Phone: +33 (0)6 02 10 71 32
Email: contact@fseindustry.com
Address
6 Chemin du vieux colombier
83130 LA GARDE
France